Die Absaugung der DeWALT DWE 7492 ist so konzipiert, dass man sowohl oberhalb des Sägeblattes, als auch unterhalb des Sägeblattes ein Anschluss für den Sauger ist. Schließt man an beiden Enden einen Staubsauger an, so funktioniert die Absaugung sehr zuverlässig und nahezu alle Späne landen im Sauger. Allerdings werden die wenigsten zwei Staubsauger in der Werkstatt haben, so dass hier eine Lösung her muss. In diesem Beitrag zeige ich euch mehrere Möglichkeiten, wie ihr die Absaugung umsetzen könnt.
Inhaltsverzeichnis
- Material für die Absaugung der DeWALT DWE 7492
- Werkzeug für die Absaugung der DeWALT DWE 7492
- Absaugung der DeWALT DWE7492* mittels DWV9470 AirLock Schlauchadapter*
- Absaugung der DeWALT DWE7492* mittels 3D-Druck
- Persönliche Meinung zu den von homewerken gelieferten Teilen
- Gegenüberstellung von Vor- und Nachteilen
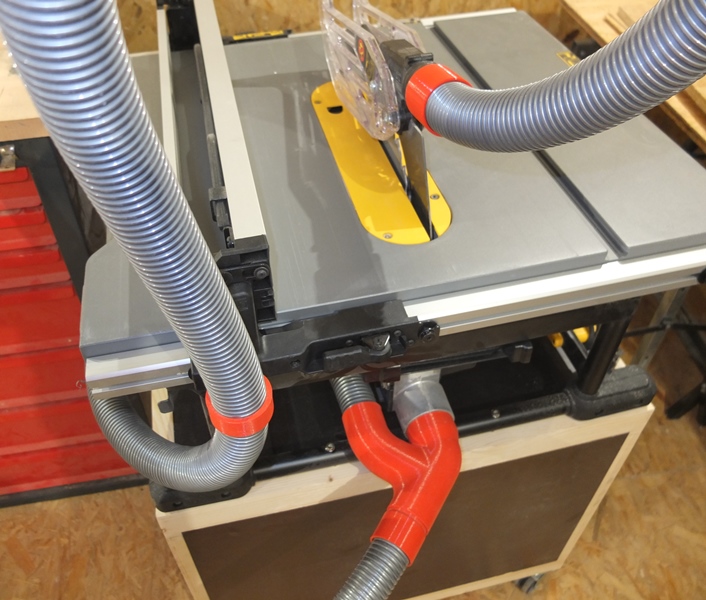
Projekt: Absaugung der DeWALT DWE 7492
Aufwand: ca. 10 Minuten
Kosten: 70-80€
Schwierigkeit: Leicht
Material für die Absaugung der DeWALT DWE 7492
Lösung von DeWALT
Lösung mittels 3D-Druck
- Staubsaugerschlauch Ø36mm* (mindestens 3Meter)
- Absaugadapter (gedruckt) bzw. Absaugadapter (STL-Filedownload)
Werkzeug für die Absaugung der DeWALT DWE 7492
Absaugung der DeWALT DWE7492* mittels DWV9470 AirLock Schlauchadapter*
Vorab muss ich sagen, dass ich mich für die zweite Variante entschieden habe. Ich wollte zuerst den DWV9470 AirLock Schlauchadapter* kaufen. Allerdings bin ich dann auf die zweite Lösung gestoßen, welche mich mehr überzeugt hat. Nichtsdestotrotz sieht der DWV9470 AirLock Schlauchadapter* mehr als solide aus und ist definitiv eine sehr gute Lösung. Nachfolgend möchte ich die Vorteile dieser Lösung, welche ich sehe, den Nachteilen gegenüberstellen.
Die Gegenüberstellung basiert rein auf Beschreibungen und Bilder, welche ich angeschaut habe. Den DWV9470 AirLock Schlauchadapter* hatte ich nie selbst in der Hand.
Gegenüberstellung von Vor- und Nachteilen
Vorteile
- Von DeWALT bereitgestellte Erweiterung => getestet und validiert
- Gute Schlauchlänge
- (Vermutlich) Sehr gut sitzende (Gummi-) Anschlüsse
- Garantie
Nachteile
- Das Adapterende, welches mit dem Staubsauger verbunden wird, wirkt verhältnismäßig klein
- Preis
- Oberer Schlauchanschluss hängt mittig über Arbeitstisch
Als wichtigsten Vorteil bei dieser Absaugung der DeWALT DWE7492* würde ich die guten Anschlüsse sehen. Damit dürfte sichergestellt sein, dass die Schläuche halten, selbst wenn Zug auf die Schläuche kommt bzw. es vibriert.
Aus meiner Sicht der größte Nachteil ist, dass der Schlauch zum oberen Saugstutzen mittig hinter dem Sägentisch herunterhängt. Bei längeren Werkstücken, welche gesägt werden sollen, befürchte ich, dass der Schlauch stört und ein Sägen in einem Zug zumindest deutlich erschweren könnte. Es könnte sein, dass die Schlauchlänge reicht, um den Schlauch z.B. über den Parallelanschlag legen zu können. Das konnte ich leider nicht validieren.
Absaugung der DeWALT DWE7492* mittels 3D-Druck
Durch Zufall bin ich auf die 3D Druckteile von homewerken.de gestoßen. Rein von der Idee her, finde ich die Lösung sehr überzeugend. Der Schlauch ist sauber verstaut und stört nicht beim sägen. Preislich nimmt sich diese Lösung allerdings wenig gegenüber dem DWV9470 AirLock Schlauchadapter*.
Wichtig ist, dass ihr den verlinkten Staubsaugerschlauch Ø36mm* verwendet, da die Gewinde der Adapter auf diesen Schlauch angepasst sind. Scheinbar reichen 2m des Schlauches. Ich würde euch aber empfehlen 3m zu nehmen. 2m scheinen mir recht knapp zu sein. Alle Bilder die ihr nachfolgend seht, sind mit 3m des Staubsaugerschlauches* gemacht.
Die 3D-Druck Teile
Y-Verbinder
Das mit Abstand wichtigste Teil ist sicherlich der Y-Verbinder. Er passt auf den unteren Sauganschluss. Gefühlt dürfte der Saugausgang für den unteren Sauganschlagg aber etwas kleiner sein, damit er strammer sitzt. Der Sauger bzw. der Saugerschlauch und der zusätzliche Verbinden passen sauber auf die jeweiligen Anschlüsse.
Innerhalb des Y-Stückes, in dem Abzweig zur unteren Absaugung hin, ist eine Verjüngung. Diese soll sicherstellen, dass die Saugleistung des langen Schlauches (~2.5m) zur oberen Absaugung hin, der Saugleistung des unteren Saugeranschlusses, ähnlich ist. Ich könnte mir vorstellen, dass dies gut funktioniert. Nachprüfen kann ich es leider nicht. Allerdings funktioniert die Absaugung sehr gut, was eindeutig für das Design spricht.
Halterung Parallelanschlag
Die Halterung für den Parallelanschlag sitzt relativ fest am Schlauch. Das hat den Vorteil, dass der Schlauch während dem Sägen oder Verfahren des Parallelanschlags nicht durchrutscht. Der Nachteil daran ist, dass das „Einfädeln“ des Schlauches nicht ganz einfach ist. Aber es ist definitiv machbar. Dennoch muss man etwas aufpassen, dass man die Schlauchhalterung nicht zerbricht.
Um den Adapter am Parallelanschlag befestigen zu können, benötigt ihr noch eine Schraube. Die Originalschraube ist zu kurz. Ich habe eine M4x20 gewählt, welche ich rumliegen hatte. Allerdings musste ich den Kopf etwas abfeilen, weil er zu breit war. Falls ihr nichts rumliegen habt, fahrt am besten in den nächsten Baumarkt und holt euch eine. Bestellen macht wegen einer Schraube keinen Sinn.
Das Festschrauben der Halterung ist etwas fummelig, da das Schraubenloch genau mittig im Ring drin sitz. Leider lässt sich das konstruktiv nicht ohne weiteres ändern. Schlussendlich schraubt man die Halterung ja nur ein Mal hin. Von daher fällt das für mich weniger ins Gewicht. Ich habe es mit einem abgewinkelten Bithalter* festgeschraubt. Das ging schlussendlich doch ganz passabel.
Adapter oberer Absauganschluss
Zum Adapter für den oberen Absauganschluss gibt es relativ wenig zu sagen. Schlauch drauf drehen, anstecken, fertig. Der Adapter passt sehr gut, sowohl in den Schlauch, als auch auf den Absauganschluss.
Achtet beim aufdrehen des Schlauches lediglich darauf, dass es sich um ein Linksgewinde handelt. Ihr müsst den Adapter also entgegen der „gewohnten“ Art auf den Schlauch drehen.
Persönliche Meinung zu den von homewerken gelieferten Teilen
Die Druckqualität war leider nicht überragend. Ich habe bereits deutlich besser gedruckte 3D-Teile in den Händen gehalten. Außen fehlen z.T. einzelne/mehrere Druck-Bahnen teilweise. Innen gab es viele nicht sauber platzierte Bahnen, welche quer durch die Saugöffnung hindurch gingen. Das ist nichts, was wirklich störend ist bzw. was sich nicht beheben lässt. Dennoch würde ich es, hätte ich einen 3D Drucker, selber machen und hätte nur die STL-Files gedownloaded. Alternativ kann man sich auch die STL-Files downloaden/bestellen und die 3D-Druckteile bei 3D-Druck-Lohnfertigern bestellen.
Einfach zur Info: Ich habe PLA als Material gewählt. Die Teile wirken sehr stabil für den Zweck.
Nachfolgende Bilder sind entstanden, nachdem die Adapter schon mehrere Projekte „gesehen“ haben. Außerdem habe ich einen Großteil der innenliegenden Fäden bereits entfernt.
Gegenüberstellung von Vor- und Nachteilen
Vorteile
- Schlauch stört nicht beim sägen
- Gutes/kreatives Design
Nachteile
- Adapter, vor allem der der unteren Absaugung, hält nicht ganz so fest
- Verarbeitung der Adapter nicht ganz perfekt (bei mir, wenn man es bei „homewerken“ bestellt)
Der größte Vorteil dieser Lösung ist meiner Meinung, dass der Schlauch aus dem Weg ist und niemals beim sägen stört. Als größter Nachteil empfinde ich, dass der Y-Adapter hin und wieder herausrutscht. Das liegt hauptsächlich daran, dass die 3D gedruckten Teile eine relativ glatte Oberfläche haben. Der Reibkoeffizient zum metallenen Ansaugstutzen dürfte klein sein. Die Toleranzen der gedruckten Teile passen allerdings gut. Ich werde mal probieren, etwas Teflonband* um den Ansaugstutzen zu wickeln. Dadurch erhoffe ich mir, dass der Ansaugstutzen dann besser hält. Ich werde von meinen Erfahrungen berichten.
Für welche Lösung entscheidet ihr euch und wieso? Lasst gern euere Kommentare hier, ich bin gespannt. Vielleicht seht oder findet ihr ja noch weitere Lösungen oder Vor- und Nachteile der beschriebenen Lösungen. Ich nehme eure Lösungen/Ideen/Punkte gerne mit auf, damit andere auch davon profitieren können.
Bist du auf der Suche nach weiteren sinnvollen Erweiterungen für die DeWALT DWE7492*, dann schau doch mal auf dieser Seite vorbei.