Bisher habe ich noch keine zufriedenstellende flexible Lösung für die Erweiterung der DeWALT DWE7492* um einen Frästisch gefunden. Mein „Problem“ ist, dass meine Werkstatt relativ klein ist und ich daher gerne die Möglichkeit hätte, die DeWALT DWE7492* möglichst „kompakt“ lagern zu können. Eine fixe Konstruktion neben der eigentlichen Säge ist daher für mich keine Option. Der Frästisch muss einfach ein- und ausgebaut werden können. So ist nachfolgende Lösung entstanden. Diese will ich euch in diesem Beitrag vorstellen.
Die verwendete Einlegeplatte ist eine universelle Einlegeplatte und passend für viele Oberfräsen*. Ich habe die Makita RT0700CX2J* und kann bestätigen, dass die Oberfräse* an der Einlegeplatte* fixiert werden kann. Die Frästischerweiterung könnt ihr selbstverständlich mit jeder anderen Platte ebenfalls nachbauen.
Vorab: Ich habe lange überlegt, welche Tischkreissäge ich mir kaufen soll. Zur Auswahl standen eigentlich nur die Bosch GTS 10 XC* und eben die DeWALT DWE 7492*. Der Vorteil der Bosch ist ganz klar die große Anhängerschaft und die bestehenden Ideen und Anleitungen um die Bosch zu erweitern. Die deutlich neuere DeWALT bietet da (bisher) wesentlich weniger Ideen. Gleichwohl lesen sich die technischen Daten der DeWALT deutlich besser. Besonders hervorzuheben sind die doppelte Staubabsaugung (oben und unten), sowie der überragende Parallelanschlag. Daher habe ich mich für die DeWALT DWE7492* entschieden.
Inhaltsverzeichnis
- Material für den DeWALT DWE7492 Frästisch
- Werkzeug für den DeWALT DWE7492 Frästisch
- Technische Zeichnungen zum Bau des DeWALT DWE7492 Frästisches
- Durchführung
- Vorab
- Gleitschienen vorbereiten
- Siebdruckplatte vorbereiten
- Rahmenteile vorbereiten
- Halterungen vorbereiten
- Gewindestangen* kürzen
- Kurze Rahmenteile an DeWALT DWE7492* Frästisch anbringen
- Lange Rahmenteile an DeWALT DWE7492* Frästisch anbringen
- Ausstülpungen ausnehmen
- Rahmen komplett fixieren
- Halterungen anbringen
- Gleitschienen anbringen
- Fräskorb montieren
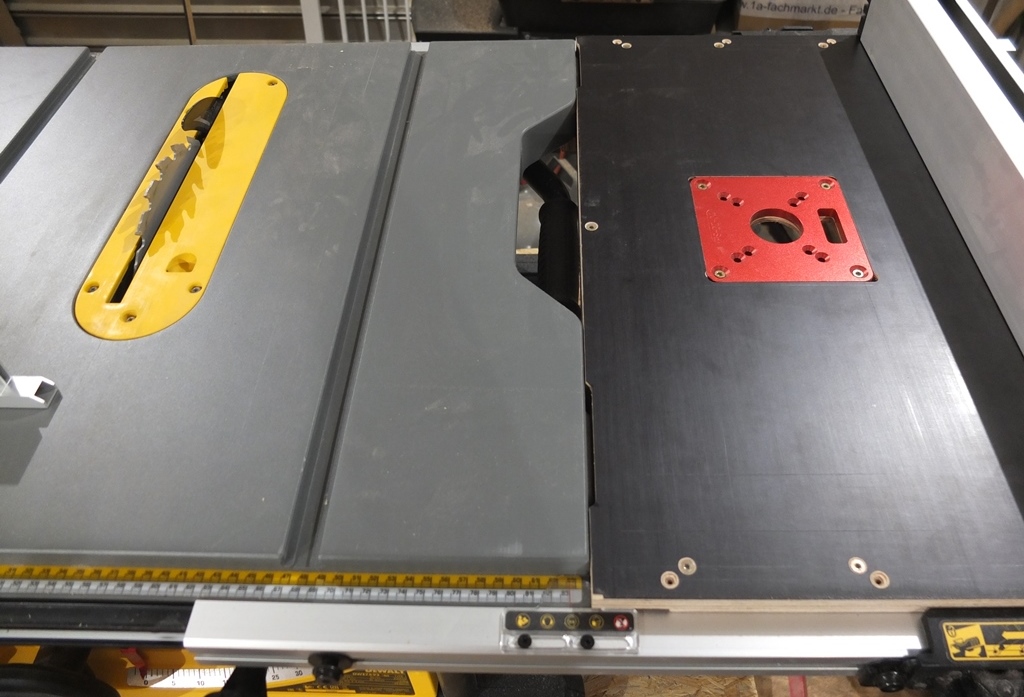
Projekt: DeWALT DWE7492 Frästisch
Aufwand: ca. 4-5 Stunde
Kosten: ~100€
Schwierigkeit: Mittel – Anspruchsvoll
Material für den DeWALT DWE7492 Frästisch
- Siebdruckplatte 125 x 30 cm, 15mm* (1x)
- Einlegeplatte Universal Oberfräse* (1x)
- Spanplattenschrauben mit Senkkopf, 4 x 40mm, 1000 Stück* (1x)
- Spanplattenschrauben mit Senkkopf, 4 x 30mm, 1000 Stück* (1x optional)
- Rahmenholz gehobelt 54x34mm* (1x)
- Exzenterhebel 2 Stück* (2x)
- M6 Gewindestange* (1x)
- Sechskantmuttern M6, 100 Stück* (1x)
- Unterlegscheiben M6, 250 Stück* (1x)
- Universalschraube mit Senkkopf, 4 x 12 mm, 1000 Stück* (1x optional)
- M4 x 20 Senkkopfschrauben, 25 Stück*
Werkzeug für den DeWALT DWE7492 Frästisch
- DeWALT DWE7492 Tischkreissäge*
- Makita RT0700CX2J Oberfräse*
- Kappsäge Metabo KGS 254 M*
- Exzenterschleifer Metabo SXE450*
- Mehrzwecksauger*
- Tiefenmesser* oder Messschieber*
- Akkuschrauber*
- Bosch Schrauberbitsatz*
- Holzbohrerset mit Aufstecksenker*
- Fräser Set 8mm Schaft*
- Streichmaß*
- 2x Schraubzwinge*
- Bohrständer*
- Scharnierbohrer*
- Mehrkranzlochsäge*
- Multitool GOP 40-30*
- Bosch Stichsäge PST 650*
- Bosch Winkelschleifer GWS 1400* mit Trennscheibe 125mm, 25 Stück* und Schruppscheiben 125mm, 5 Stück*
Technische Zeichnungen zum Bau des DeWALT DWE7492 Frästisches
Gleitschiene
Siebdruckplatte (Frästisch)
Vorsicht, Aussparungen, welche hier ausgenommen werden, fehlen in den Zeichnungen.
Rahmenteile
Vorsicht, Aussparungen, welche hier ausgenommen werden, fehlen in den Zeichnungen.
Halterungen
Folgt…
Durchführung
Vorab
Ich habe den Frästisch in einer etwas anderen Reihenfolge gebaut, als ich es hier beschreibe. Das hat den Grund, dass mein Vorgehen nicht ganz optimal war und ich euch das, in meinen Augen, beste Vorgehen zeigen möchte. Daher kann es aber sein, dass auf einzelnen Bildern bereits Teile am Frästisch zu sehen sind, welche ihr eventuell erst in einem späteren Schritt baut/anbringt bzw. welche ihr bereits angebracht habt und bei mir noch fehlen. Darüber müsst ihr euch also keine Gedanken machen.
So, genug gebabbelt, kommen wir zur eigentlichen Anleitung.
Gleitschienen vorbereiten
Anfangen werden wir mit den Gleitschienen für den Frästisch der DeWALT DWE7492*, also die im Bild unten gezeigten Leisten. Ihr benötigt zwei davon.
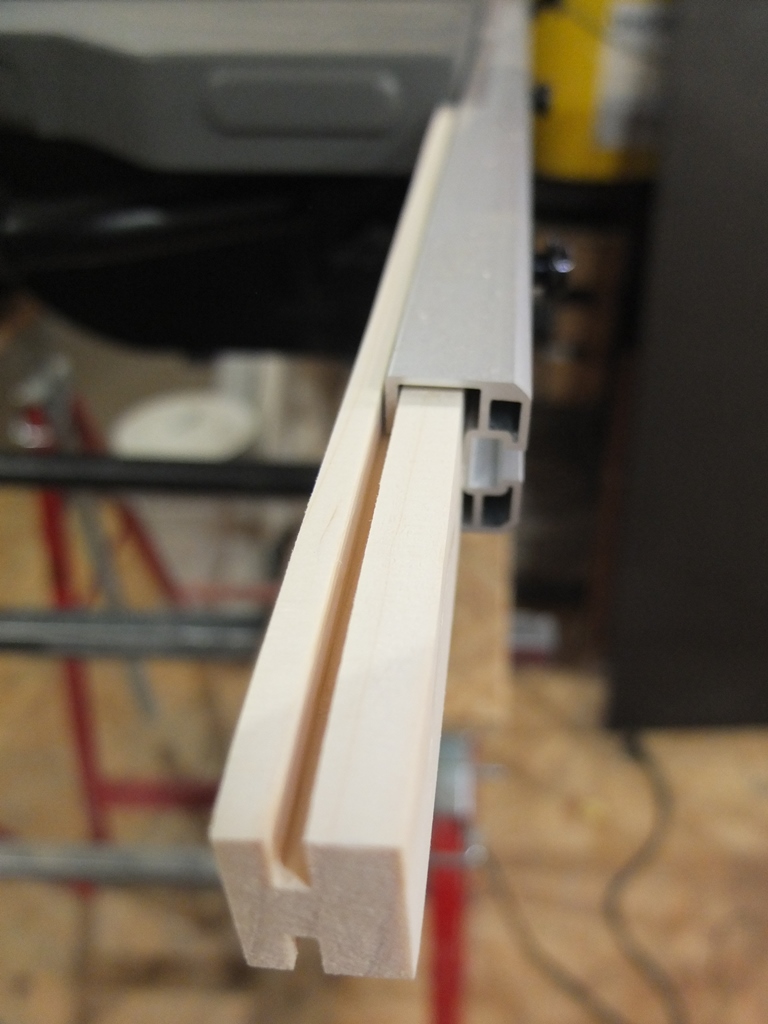
Hier müsst ihr gleich genau arbeiten. Aber dafür habt ihr ja die DeWALT DWE7492* gekauft. Zunächst nehmt ihr euch ein Stück Holz. Ich hatte noch einen Resten Rahmenholz gehobelt 54x34mm* zur Hand. Schlussendlich seid ihr aber relativ frei, in dem was ihr wählt. Es muss aber mindestens 2,75cm hoch, 4cm breit und 30cm lang sein.
Als erstes bin ich einmal schnell mit dem Exzenterschleifer* darüber gerutscht (100er oder 120er Schleifpapier) und habe die gröbsten Unebenheiten entfernt.
Danach kürzt ihr das Holz* mit der DeWALT DWE7492* oder besser mit einer Kappsäge* auf 30cm.
Eine hilfreiche Erweiterung für eure Kappsäge* könnte das Nachrüsten eines Sanftanlaufes sein.
Das 30cm Holzstück* wird jetzt passend zugeschnitten, dass es in die Führungsschiene der DeWALT DWE7492* passt. Dazu reduziert ihr die 3,4cm breite Seite mit der DeWALT DWE7492* auf 2,75cm.
Jetzt wird noch die 54mm lange Seite in zwei 17mm lange Seiten geschnitten. Nun habt ihr also zwei 30cm lange Holzstücke, mit einer Kantenlänge von 2,75 x 1,7cm. Diese beiden Stücke werden die Gleitschienen. Den wenige Millimeter breiten Rest benötigt ihr nicht mehr.
Jetzt noch einmal schnell von Hand oder mit einem Schleifgerät* über die Leisten schleifen. Nehmt jetzt ein feineres Schleifpapier, je nachdem, was ihr zur Hand habt (Körnung >=160).
In die Gleitschienen müssen nur noch die Aussparungen der Führungsschiene ausgenommen werden. Wenn man nachmisst, passt eine Sägeblattbreite der DeWALT DWE7492* (Standardsägeblatt ~ 3mm) genau.
Ihr stellt den Parallelanschlag der DeWALT DWE7492* auf 6,1cm ein und klappt die Hilfe für dünne/kleine Schnitte herunter. Der Abstand zwischen Sägeblatt und Parallelanschlag sollte jetzt ~1,05cm betragen (Bitte nachprüfen!). Stellt jetzt noch die Schnitttiefe von 1cm mit einem Tiefenmesser* oder Messschieber* ein. Überprüft nochmal den Abstand zwischen Sägeblatt und Parallelanschlag. Danach kann es losgehen.
Schneidet in die vorbereiteten Holzleisten hochkant (! wichtig, sonst geht es euch wie mir und ihr macht die Übung noch einmal 🙂 ) die Führungsnuten hinein. In jedes Holzstück kommt zunächst eine (!) Führungsnut hinein. ). Stellt jetzt die Schnitttiefe von 8,5mm mit einem Tiefenmesser* oder Messschieber* ein. Jetzt schneidet ihr die zweite Führungsnut in jede Holzleiste. Achtet darauf, dass die Führungsnuten genau übereinander sind.
Wenn ihr die Leisten „falsch“ dreht, sind die Führungsnuten versetzt und die Gleitschiene ist für die Tonne. Jetzt sollten die Gleitschiene wie in den Bildern unten aussehen und sich gut in der Führungsschiene hin und her bewegen lassen. Sollte das nicht der Fall ist, müsst ihr ggfs. noch an der ein oder anderen Stelle etwas nachsägen. Achtet darauf, dass die weniger tiefe Nut unten ist. Bitte dies auch später bei der Montage beachten!
Hier hab ich noch ein Bild bei dem ihr eine falsch gesägte Gleitschiene (rechts) und eine richtig gesägt Gleitschiene (links) seht. Theoretisch würde die rechte Gleitschiene auch gehen. Allerdings ist der Steg vom seitlichen zum oberen Steg sehr schmal so dass die Bruchgefahr sehr groß ist.
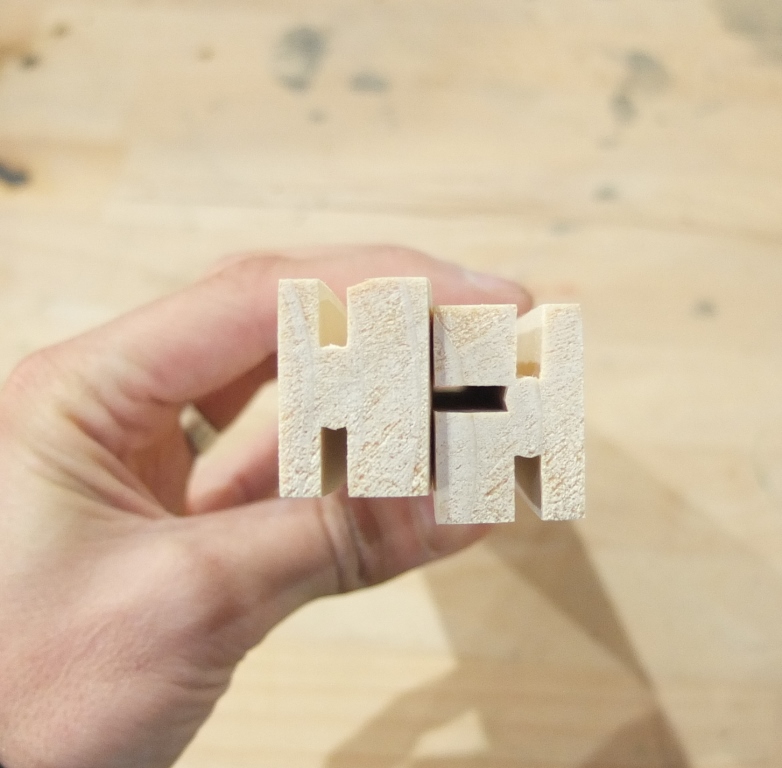
Siebdruckplatte vorbereiten
Siebdruckplatte zuschneiden
Nachdem die Gleitschienen vorbereitet sind, geht es jetzt zur Siebdruckplatte. Zunächst schneiden wir die Siebdruckplatte mit der DeWALT DWE7492* auf die finalen Maße. Die Breite ist dabei flexibel. Ich habe mich dazu entschieden, die Platte 30cm breit zu machen. Die Länge der Platte ist fix und sollte genau auf 58,4cm gekürzt werden.
Wenn ihr die Platte zugeschnitten habt, könnt ihr die Siebdruckplatte probeweise auf die Maschine legen. Fahrt dazu den Parallelanschlag der DeWALT DWE7492* relativ weit aus. Die Siebdruckplatte legt ihr auf die Profilschienen, an denen der Parallelanschlag festgemacht ist. Die Siebdruckplatte sollte sowohl in der Höhe als auch in der Breite unter dem Parallelanschlag hindurch passen. Wenn das nicht der Fall ist, müsst ihr entweder den Parallelanschlag etwas anheben oder an den Kanten der Siebdruckplatte, in dem Bereich, in dem die Siebdruckplatte auf der Profilschienen aufliegt, etwas Material abfräsen.
Schnittmaßanzeige aus Siebdruckplatte ausnehmen
Jetzt, nachdem die Siebdruckplatte zugeschnitten ist, müssen noch mehrere Sachen ausgenommen werden.
- Schnittmaßanzeige
- Einlegeplatte* für die Oberfräse*
- Abstandshalter an der DeWALT DWE7492*
Wir beginnen mit der Schnittmaßanzeige. Wenn man den Parallelanschlag der DeWALT DWE7492* ganz ausfährt, steht die Schnittmaßanzeige etwas über den Arbeitstisch der DeWALT DWE7492* hinaus. Im Bild unten entspricht das dem rot markierten Bereich.
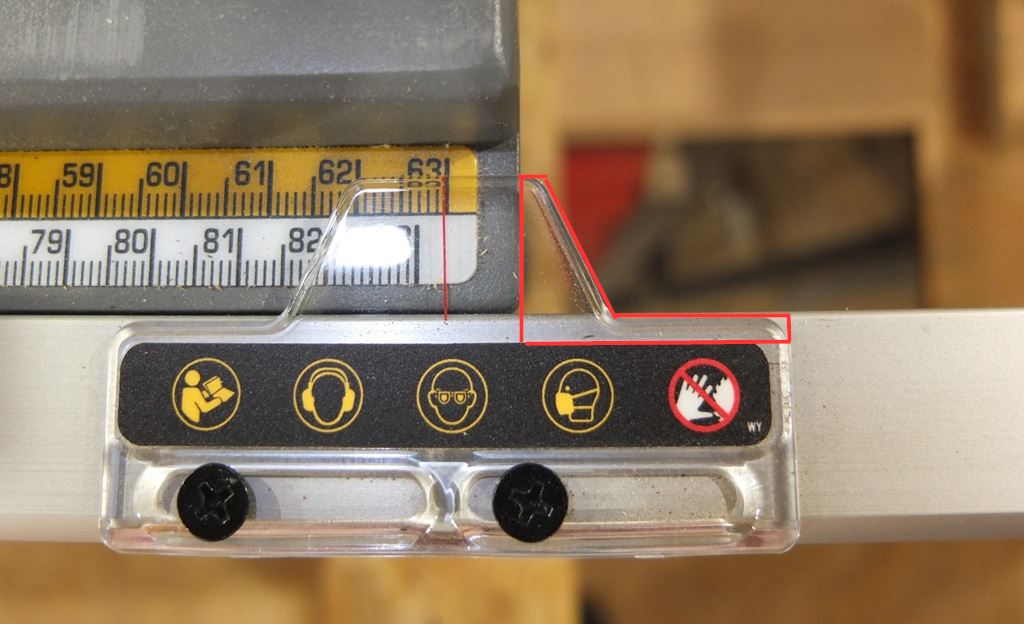
Da der Frästisch auf den Alu Profilschienen aufliegt, muss auch in diesem Bereich etwas ausgenommen werden. Prinzipiell müsst ihr hier nicht 100% exakt arbeiten, da man das später kaum sieht.
Zunächst zeichnet ihr euch den Bereich, den ihr ausnehmen wollt mit dem Streichmaß* und einem Stift (z.B. Bleistift) an. Die gesamte Aussparung ist 2,7cm lang. Im dünnen Bereich (1,7cm lang) müsst ihr mindestens 3mm Breite ausnehmen. Innerhalb von 5mm steigt ihr von den 3mm auf 18mm Breite. Die 18mm Tiefe haltet ihr bis zum Rand der Siebdruckplatte.
Nachdem der auszunehmende Bereich angezeichnet ist, nehmt ihr eure Oberfräse* und einen kleinen Nutfräser (z.B. 10mm) aus dem Fräser Set*. Stellt eine Frästiefe von 4mm ein (Schnittmaßanzeige ist 3mm hoch) und nehmt die angezeichnete Fläche aus.
Einlegeplatte* für die Oberfräse* aus Siebdruckplatte ausnehmen
Als nächstes nehmen wir die Einlegeplatte* für die Oberfräse* aus. Wenn ihr eine Kopierschablone habt, nehmt ihr natürlich diese zur Hand. Leider besitze ich (noch => Zukunftsprojekt?) keine. Es geht auch ohne, ist aber etwas aufwändiger und fehleranfälliger.
Zunächst legt ihr die Einlegeplatte* mittig (genau ausmessen) auf die glatte Seite der ausgeschnittenen Siebdruckplatte. Zeichnet den Rand nach (z.B. mit Bleistift).
Da wir mit der Kopierhülse der Oberfräse* arbeiten, müsst ihr als nächstes einen Nutfräser aus dem Fräser Set* auswählen. Ich habe wieder den Nutfräser mit dem Fräsdurchmesser von 10mm gewählt. Montiert die große Kopierhülse (Außendurchmesser 16mm) auf dem großen Fräskorb. Die Differenz zwischen Fräser Außendurchmesser und Kopierhülse (Außendurchmesser) beträgt insgesamt 6mm, bzw. 3mm pro Seite. Zeichnet daher um das markierte Viereck für die Einlegeplatte* nochmal ein um 3mm größeres Viereck/Markierungen (siehe Bilder unten).
Wenn ihr eine Kopierschablone besitzt, so legt ihr diese an die äußeren Markierungen an und befestigt sie mit Schraubzwingen* an der Werkbank. Wenn ihr keine Kopierschablone besitzt, nehmt ihr einfach Holzreste. Absolut entscheidend ist, dass diese gleich dick und plan sind, damit das, was ihr ausfräst, gleichmäßig tief wird. Außerdem muss jeweils eine Kante gerade sein.
Am besten eignen sich da z.B. Reste von Siebdruck- oder OSB-Platten. Ihr benötigt zwischen zwei und vier Resten. Ich habe nur zwei zur Hand. Daher muss ich mehrmals umbauen.
Legt die Siebdruckplatten genau an die Markierungen einer Ecke des äußeren Vierecks und fixiert diese gut mit Schraubzwingen*. Bleibt mit den Schraubzwingen* mindestens 10cm von der Fräskante weg, damit ihr gut arbeiten könnt.
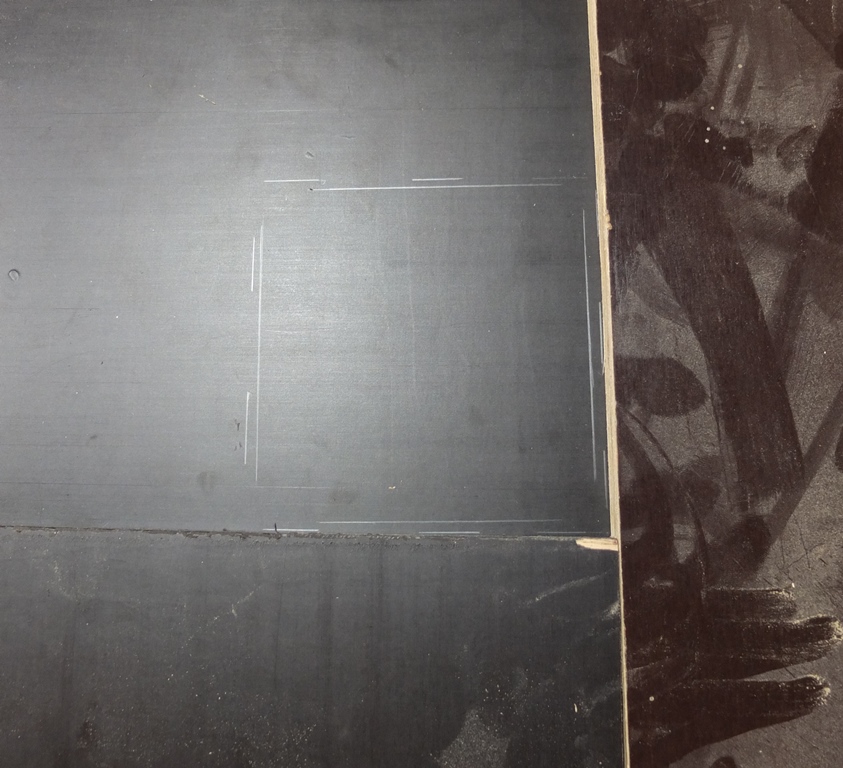
Jetzt geht es ans ausfräsen. Meine Einlegeplatte* ist 8mm dick. Stellt also eine Frästiefe von 8mm oder minimal mehr (8,1-8,4mm) ein. Optimal ist, wenn die Platte genau bündig zur Siebdruckplatte ist. Allerdings ist eine minimal versenkte Einlegeplatte* auch verkraftbar.
Setzt also die eingestellte Oberfräse* an und fräst 1-2cm. Setzt nochmal ab und messt die Frästiefe mit einem Tiefenmesser* oder Messschieber* nach. Das wiederholt ihr so lange, bis die Frästiefe genau passt!
Wenn ihr die Frästiefe richtig eingestellt habt, fräst ihr langsam los und fahrt Stück für Stück die ganz Fläche ab. Je nachdem müsst ihr die Siebdruckplatten, welche ihr als Rahmen benutzt, mehrmals umsetzen. Lasst euch dabei genug Zeit und arbeitet sauber. Dies ist eine mit der wichtigsten Arbeitsschritte bei dieser Anleitung.
Wenn ihr die Fläche ausgefräst habt, macht ihr natürlich den Einlegetest. Es sollte in etwa so aussehen.
Löcher für die Einlegeplatte* der Oberfräse* bohren und Einlegeplatte befestigen
Jetzt müssen die Löcher noch gebohrt werden. Legt dazu die Einlegeplatte* in die ausgefräste Fläche. Richtet sie mittig aus (sollte sie etwas Spiel haben) und fixiert sie mit einer Schraubzwinge*. Schraubt jetzt die 12 diagonalen Löcher mittels Bohrständer* und Scharnierbohrer*. Die inneren acht Löcher könnt ihr dann mit einem 6mm Holzbohrer durchbohren. Wichtig ist, dass ihr die äußersten vier Löcher nicht mit dem Holzbohrer durchbohrt. Zeichnet jetzt noch das Viereck an.
Danach könnt ihr die Schraubzwinge* lösen und die Einlegeplatte* herausnehmen. Zeichnet auf der Rückseite die Diagonale ein um den Mittelpunkt zu bekommen. Im Mittelpunkt bohrt ihr mit der Mehrkranzlochsäge* ein 45mm oder 50mm Loch. Das Loch in der Einlegeplatte* hat einen 40mm Durchmesser. Gebt da ruhig etwas Luft.
Jetzt fehlt eigentlich nur noch das Viereck. Ich habe es mittels vier Löchern an den Ecken und einer Stichsäge ausgeschnitten. Ehrlich gesagt, auch wenn man es später kaum mehr sieht, ist das Loch bei mir schäbig geworden. Ich würde euch daher empfehlen, besser ein Multitool* zu verwenden. Daran habe ich leider erst später gedacht. Auch hier gilt, dass ihr das Viereck ruhig 2-3mm größer Ausschneiden dürft. Etwas Luft schadet hier nicht. Das macht euch das spätere Einführen etwas einfacher.
Zu guter Letzt legt ihr die Einlegeplatte* wieder ein. In die äußeren 4 Löcher schraubt ihr jeweils eine Schraube 4 x 12 mm*. Achtet darauf, dass die erste Schraube die Einlegeplatte* nicht verschiebt. Alternativ zu den 4 x 12 mm* Schrauben könnt ihr auch längere Schrauben verwenden und den überstehenden Teil vorsichtig abflexen.
Rahmenteile vorbereiten
In der Summe benötigen wir vier Rahmenteile jeweils aus den Resten der Siebdruckplatte* ausgeschnitten:
- 3 x 30cm (2x)
- 3 x ca. 55cm (genaues Maß wird später bestimmt)
- 4,5 x ca. 55cm (genaues Maß wird später bestimmt)
Diese Streifen könnt ihr mit eurer DeWALT DWE7492* zuschneiden. Damit sind die Rahmenteile soweit wie nötig vorbereitet.
Halterungen vorbereiten
Um den Frästisch an der Kreissäge fixieren zu können, benötigt es noch zwei Halterungen. Diese bereiten wir abschließend noch vor, bevor es an den Zusammenbau geht.
Um die nachfolgenden Erklärungen besser zu verstehen könnt ihr auch einen kurzen Blick auf die technischen Zeichnungen werfen.
Die beiden Halterungen solltet ihr ebenfalls aus den Resten der Siebdruckplatte* ausschneiden können. Diese haben folgende Maße:
- 17 x 4cm
- 8 x 3,4cm
Bei der größeren Platte müsst ihr zusätzlich ein 1,5cm tiefes und 4cm breites Stück beginnend 3,5cm vom Rand ausnehmen. Zeichnet dies zuerst mit dem Streichmaß* an und sägt es dann mit der Stichsäge* aus.
Von beiden Platten müsst ihr noch ein 3 x17mm abfräsen um eine schöne Klemmfläche zwischen Siebdruckplatte und DeWALT DWE7492* gewährleisten zu können. Dies könnt ihr sowohl mit der Oberfräse* als auch der DeWALT DWE7492* machen.
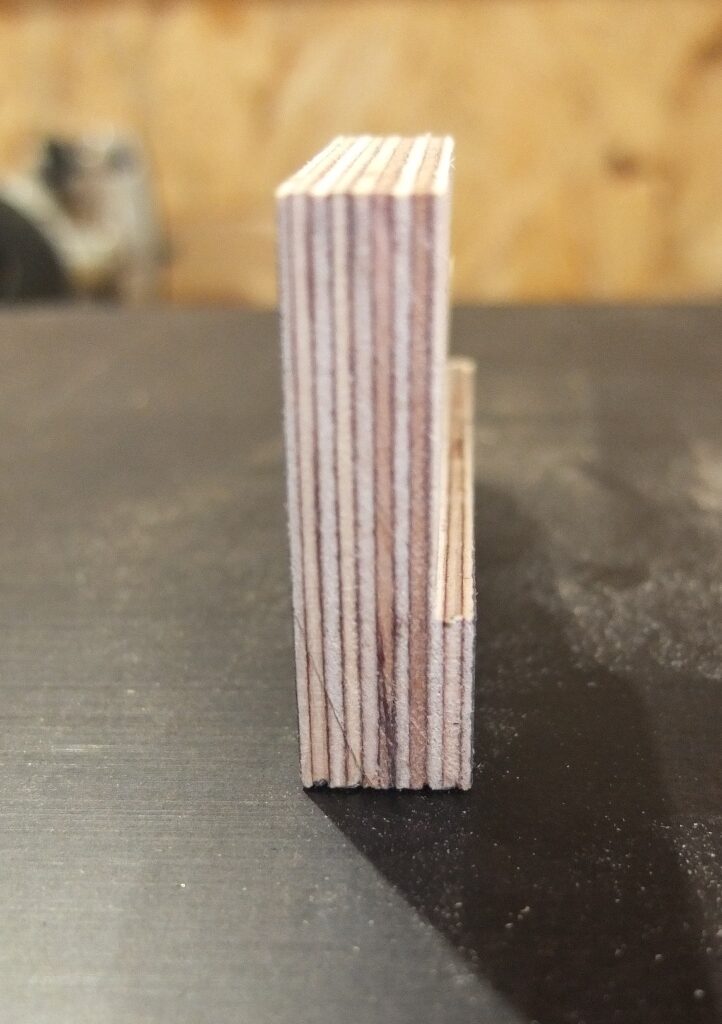
Bevor die Halterungen fertig sind, müssen noch Langlöcher gebohrt werden. Diese beginnen und enden jeweils 0,6cm vom Rand (lange Kante) entfernt. Bei der größeren Halterung kommen 2 Langlöcher hinein. Das eine 2,6cm vom Rand (recht nahe an der Vertiefung) entfernt. Auf der anderen Seite habe ich 4,5cm gewählt. Bei der kleinen Halterung kommt das Langloch mittig rein (4cm vom Rand).
Es gibt mehrere Möglichkeiten ein Langloch zu bohren. In Holz ist vermutlich eine sehr saubere Variante mittels Holzbohrer* und Multitool*. Ich habe (leider) lediglich den Bohrer verwendet, weshalb es optisch nicht ganz sauber ist. Nehmt einen 8er (oder 7er) Holzbohrer* und bohrt jeweils an den Enden ein Loch. Mittelpunktsabstand vom Rand ist 1cm. Mit dem Multitool* könnt ihr die Verbindung zwischen den Löchern ausschneiden. Wenn ihr es wie ich, ohne Multitool*, machen wollt, bohrt ihr noch zwei weitere Löcher je Langloch und entfernt die übrigen Stege.
Gewindestangen* kürzen
Als letzter Vorbereitungsschritt vor der Montage müssen die Gewindestangen* gekürzt werden. Am besten geht das mit einem Winkelschleifer* und 6x M6 Muttern. Ihr braucht 3 Gewindestangenstücke à ca.7cm. Schraubt jeweils vor und nach einer Schnittstelle (2-3 cm entfernt) eine Mutter. Trennt jetzt die Gewindestange* mit dem Winkelschleifer* und einer Trennscheibe* an den gewünschten Stellen durch. Danach bringt ihr die Schruppscheibe* an und flext die Enden im ca. 45° Winkel leicht an. Zum Schluss schraubt ihr die Muttern heraus, so dass über jedes Ende einmal eine Mutter geschraubt wurde.
Kurze Rahmenteile an DeWALT DWE7492* Frästisch anbringen
Holt euch zunächst die Siebdruckplatte mit der eingelassenen Einlegeplatte*. Entlang der 30cm langen Kanten zeichnet ihr jeweils 3 Löcher 19mm vom Rand entfernt an. Die äußeren Löcher sind dabei 5cm vom Rand, das 3. Loch ist mittig. Die Löcher bohrt ihr mit einem 3er Holzbohrer mit Aufstecksenker* vor. Wichtig ist, dass ihr genug ansenkt. Schraubt in jedes Loch eine Spanplattenschraube (4 x 40mm)* vor, so dass sie halten, aber noch nicht auf der anderen Seite heraus schauen.
Fahrt jetzt den Parallelanschlag der DeWALT DWE7492* komplett heraus, schiebt die Gleitschienen in die Alu-Profile der DeWALT DWE7492* und legt die Siebdruckplatte mit der eingelassenen Einlegeplatte* mittig auf die Alu-Profile die den Parallelanschlag halten. Achtet darauf, die Siebdruckplatte mittig auszurichten. Nehmt jetzt die beiden 30cm langen Rahmenteile und setzt diese hochkant zwischen Gleitschiene und Siebdruckplatte (siehe Bild unten). Achtet darauf, dass die Siebdruckplatte und das Rahmenteil bündig abschließen.
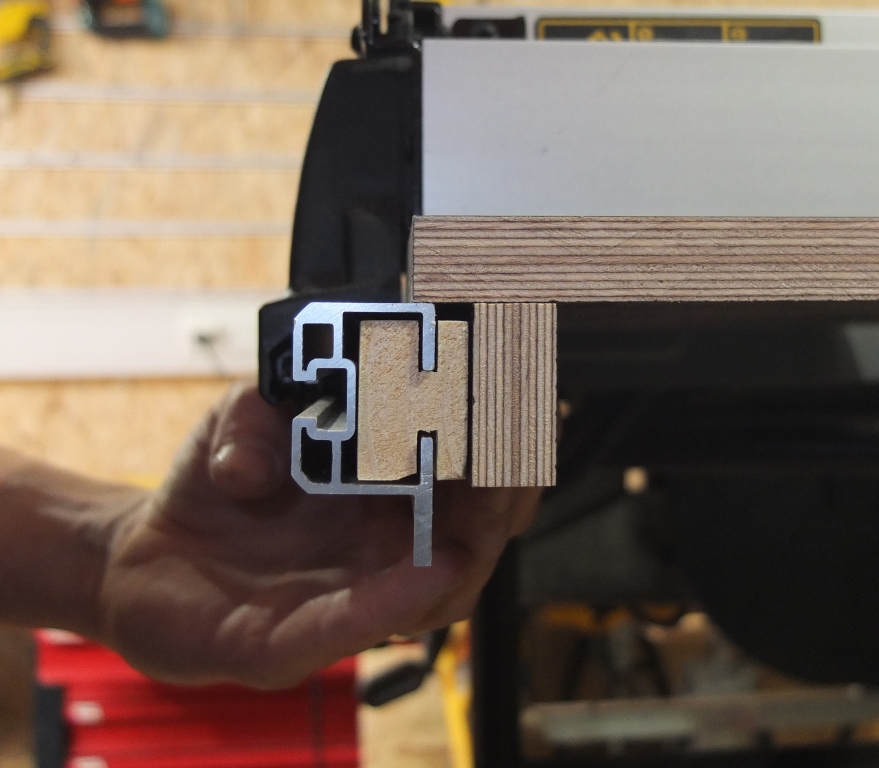
Wenn alles mittig, bündig und im Senkel ist, schraubt ihr die zwei Rahmenteile mit den sechs vorgeschraubten Schrauben an die Siebdruckplatte mit der eingelassenen Einlegeplatte*.
Lange Rahmenteile an DeWALT DWE7492* Frästisch anbringen
Jetzt messt ihr den Abstand zwischen den zwei festgeschraubten Rahmenteilen nahe an der Siebdruckplatte mit der eingelassenen Einlegeplatte*. Die beiden anderen Rahmenteile kürzt ihr mittels Kappsäge* auf die gemessene Länge, die in etwa 53,5cm betragen sollte. Welches ihr auf welcher Seite befestigt ist dabei egal.
Bevor wir die Rahmenteile festschrauben bohren wir noch 3 Löcher in das Rahmenteil, welches 4,5cm hoch ist. Spannt dazu einen 8er (oder 7er) Holzbohrer* ein. Mit dem Streichmaß* messt ihr folgende Punkte aus:
- 1cm von der langen Kante entfernt (welche ist egal), allerdings wird dies dann die Kante, welche vom DeWALT DWE7492* Frästisch weg zeigt
- 5cm vom rechten Rand weg (wenn man auf die raue Seite schaut und die 1cm Markierung unten ist)
- 4cm vom linken Rand weg (wenn man auf die raue Seite schaut und die 1cm Markierung unten ist)
Diese beiden Löcher bohrt ihr. Danach legt ihr auf das linke Loch die breite Halterung (auf Parallelität der Kanten achten) und übertragt das zweite Loch. Auch dieses bohrt ihr.
Als nächsten schrauben wir die beiden Rahmenteile an den DeWALT DWE7492* Frästisch. Zeichnet jetzt auf der Siebdruckplatte mit der eingelassenen Einlegeplatte* mittels Streichmaß* an jeder Kante jeweils zwei Löcher 10 cm von der Mitte aus an (ich habe nur 1 Loch angebracht). Diese Löcher haben einen Abstand von 7,5mm vom Rand. Auch diese Löcher bohrt ihr mit einem 3er Holzbohrer mit Aufstecksenker* vor. Schraubt in jedes Loch eine Spanplattenschraube (4 x 40mm)* vor, bringt die Rahmenteile in Position so dass sie bündig abschließen und schraubt die Schrauben fest.
Ausstülpungen ausnehmen
Die DeWALT DWE7492* hat am Rand des Arbeitstisches die in nachfolgenden Bildern gezeigten Ausstülpungen. Weshalb diese Ausstülpungen vorhanden sind ist mir nicht ganz klar. Fakt ist, dass durch diese Ausstülpungen der DeWALT DWE7492* Frästisch nicht bündig an der Arbeitsfläche anliegen, wenn wir hier nicht aktiv werden.
Legt den DeWALT DWE7492* Frästisch auf die Führungsschienen und schiebt ihn ganz an die DeWALT DWE7492*. Markiert euch die beiden Bereiche, die ihr ausfräsen müsst. Seid dabei ruhig etwas großzügig und gebt links und rechts rund 5mm-10mm Spiel.
Die Aussparung ist 3mm tief. Wir fräsen daher 4mm aus.
Montiert wieder einen Nutfräser (z.B. 10mm) in eurer Oberfräse* und stellt eine Frästiefe von rund 30mm ein. Nachfolgenden Schritt kann man z.B. auch mittels Anschlag der Oberfräse* ausführen. Ich bin nicht so ein Freund dieses Anschlags. Daher habe ich selbst eine Kante erzeugt.
Ich habe den Abstand zwischen Fräser und Fräskorb gemessen (5cm). Auf diesen Abstand rechnet ihr die 4mm Frästiefe darauf. 5,4cm vom Rand entfernt fixiert ihr ein Brett/Wasserwaage/… mit einer geraden Kante mittels 2x Schraubzwingen*. Jetzt könnt ihr zwischen den an markierten Stellen den Frästisch ausnehmen. Achtet aber auf die Fräsrichtung damit euch die Oberfräse* nicht abhaut.
Rahmen komplett fixieren
Um dem Rahmen zusätzliche Stabilität zu verleihen, verschrauben wir die einzelnen Rahmenteile untereinander. Nehmt euer Streichmaß* zur Hand und zeichnet
- 7mm (bei Rahmenteilen bei denen nichts ausgenommen ist)
- 10mm (bei Rahmenteilen mit ausgenommenen Teilen)
vom seitlichen Rand je Seite zwei Markierungen. Von oben bzw. unten lasst ihr 8mm Abstand. In der Summe sind es 8 Löcher, die ihr markiert. An diesen 8 Markierungen bohrt ihr mit einem 3er Holzbohrer mit Aufstecksenker* Löcher vor. In jedes Loch kommt eine Spanplattenschrauben mit 4 x 40mm*.
Halterungen anbringen
Als vorletzten Schritt bringen wir die Halterungen an den DeWALT DWE7492* Frästisch an. Dazu benötigen wir
- die zugeschnittenen Gewindestangen
- die beiden Halterungen
- zwei Packungen Exzenterhebel samt Zubehör*
- drei Sechskantmuttern M6*
- drei Unterlegscheiben M6*
In folgendem Bild ist der prinzipielle Aufbau dargestellt.
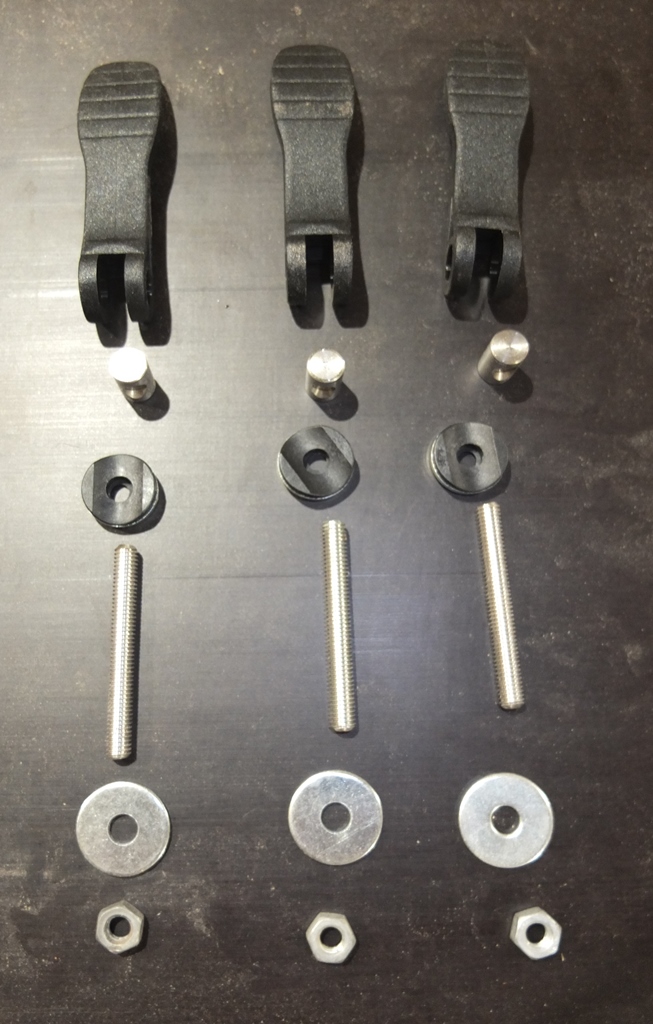
Zuerst wird der Exzenterhebel auf die Gewindestange geschraubt. Danach wird die Gewindestange durch eines der Löcher in dem 4,5cm hohen Rahmenteil gesteckt. Je nach Loch wird die passende Halterung darüber gesteckt. Wichtig ist, dass die ausgenommene Fläche der Halterungen zum Frästisch hin und Richtung Frästisch Oberseite zeigt (siehe Bilder unten). Danach wird noch die Unterlegscheibe* über die Gewindestange gesteckt und die Sechskantmutter* darauf geschraubt. Fertig sind die Halterungen.
Jetzt müsst ihr die Muttern nur noch einstellen. Scheibt dazu den DeWALT DWE7492* Frästisch über die Führungsstangen des Parallelanschlags bis zum Arbeitstisch der DeWALT DWE7492*. Die Muttern müssen genau so fest angezogen werden, dass ihr die Halter, wenn sich die Exzenterhebel* im losen Zustand befinden, gut über die Blechabkantung des Arbeitstisch der DeWALT DWE7492* bekommt. Gleichzeitig muss der DeWALT DWE7492* Frästisch an der Arbeitsplatte fixiert sein, wenn die Exzenterhebel* umgelegt (festgezogen) werden.
Gleitschienen anbringen
Jetzt fehlen nur noch die Gleitschienen, welche wir am DeWALT DWE7492* Frästisch anbringen müssen. Fahrt dazu den Parallelanschlag der DeWALT DWE7492* rund 30cm aus. Schiebt die beiden Gleitschienen in die Führungsstangen und legt den DeWALT DWE7492* Frästisch auf die Führungsstangen. Lasst beides 5-10 cm über die Führungsstangen der DeWALT DWE7492* überstehen. Schnappt euch euer Streichmaß, stellt es auf 14mm ein und macht 4cm vom hinteren Rand entfernt eine Markierung. Dies macht ihr auf beiden Seiten.
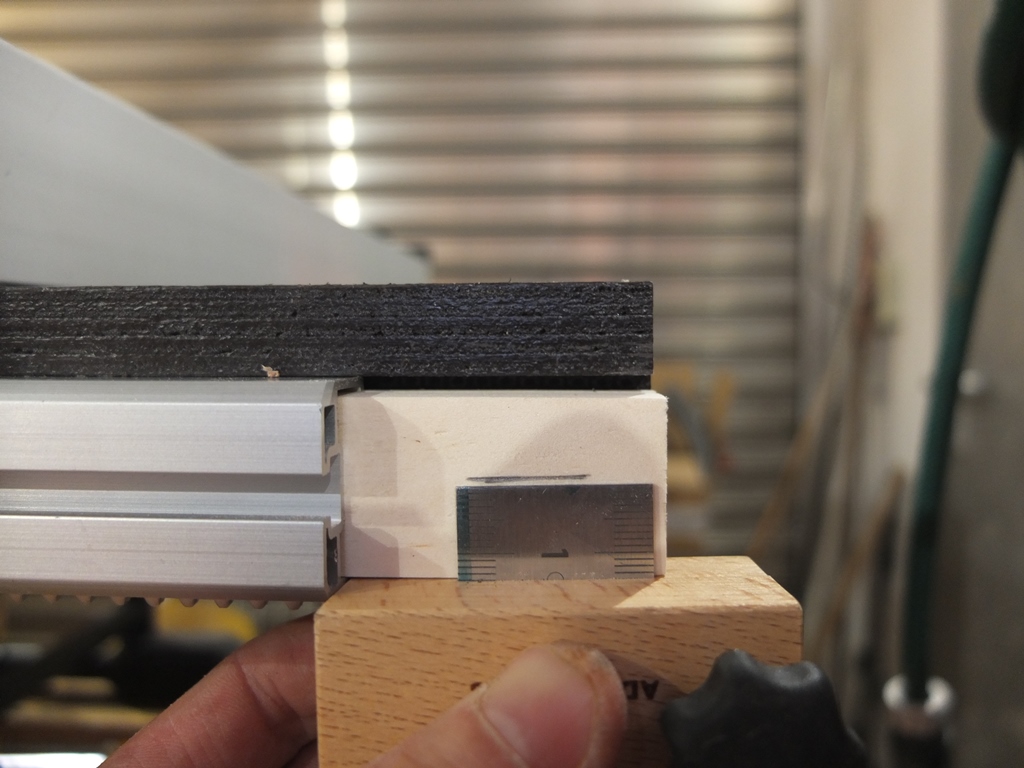
Wenn ihr schräg von hinten schaut, sollten die Markierungen auf Höhe der durchgängigen Verbindung der Gleitschiene sein, so dass die Schrauben später komplett im Holz verlaufen.
Nehmt wieder den 3er Holzbohrer mit Aufstecksenker* und bohrt auf beiden Seiten ein Loch mindestens durch die Gleitschienen, besser sogar noch rund bis zur Hälfte der Siebdruckplatte. Nehmt jetzt die Spanplattenschrauben 4x30mm* (oder die Spanplattenschrauben 4 x 40mm* => Vorsicht müssen gekürzt werden, da die Gleitschiene und Siebdruckplatte zusammen nur 35mm stark sind) und schraubt jeweils eine Schraube in die Löcher.
Vorherigen Schritt wiederholt ihr noch zwei Mal. Einmal in der Mitte vom DeWALT DWE7492* Frästisch bei 15cm. Für das letzte Loch nehmt ihr den DeWALT DWE7492* Frästisch samt Gleitschienen heraus und dreht ihn einmal um, so dass der Großteil des DeWALT DWE7492* Frästisches in den Führungsstangen sitzt (ähnlicher Aufbau wie beim 1. Loch).
Der Parallelanschlag sollte sich jetzt über den DeWALT DWE7492* Frästisch schieben lassen bzw. es sollte euch möglich sein, den DeWALT DWE7492* Frästisch unter dem Parallelanschlag hindurch zu ziehen. Sollte das sehr schwer gehen, ist es möglich, dass es die Gleitschienen zu nahe an den Rahmen gezogen hat, so dass zwischen den Führungsstangen der DeWALT DWE7492* und den Gleitschienen zu viel Spannung (und somit Reibung) herrscht. Abhilft sollte schaffen, wenn ihr die Führungsnuten in den Gleitschienen nochmal 1-2 mm breiter sägt (nicht tiefer!).
Fräskorb montieren
Um den Fräskorb montieren zu können, müsst ihr auf dessen Unterseite 4 Schrauben lösen und die schwarze Abdeckung entfernen. Danach nehmt ihr 4 M4 x 20 Senkkopfschrauben* und schraubt den Fräskorb an den neuen Frästisch.
Jetzt ist der DeWALT DWE7492* Frästisch fertig. Ich wünsche euch viel Spaß damit.
Über ein kurzes Feedback, wie euch der Beitrag gefällt freue ich mich. Außerdem bin ich über Kritik, Verbesserungsvorschläge, etc. froh und probiere diese so gut als möglich umzusetzen.
Bist du auf der Suche nach weiteren Verbesserungsmöglichkeiten für die DeWALT DWE7492*, dann schau doch mal auf dieser Seite vorbei.
15 Antworten auf „DeWALT DWE7492 Frästisch“
sag mal könnte ich die frästischplatte auch bei dir kaufen ?
beste grüße
udo
Hei Udo
So gerne ich jetzt ja sagen würde, muss ich aktuell leider ablehnen. Ich habe gerade leider viel zu wenig Zeit für Projekte jeglicher Art.
Gerade habe ich endlich den Unterschrank für die DeWALT DWE7492 fertig gebaut (Artikel dazu folgt). Allerdings war ich fast zwei Monate dran für effektiv maximal zwei Tage Arbeit. Das erste Mal benötigt es ja immer etwas länger, bis man den genauen Plan im Sack hat. Dann probiert man ja noch dies und jenes aus…
Die Kinder lassen aktuell leider nicht mehr zu.
Ich schätze deine Anfrage aber sehr und sehe das als Lob für die Arbeit an.
Wieso traust du dich nicht selber dran? Fehlt dir auch die Zeit? Bzw. ist die Anleitung zu verwirrend/unklar/verbesserungswürdig? Über Tipps/Hinweise/etc. bin ich immer sehr froh.
Viele Grüße
Andreas
Super geworden, danke für den tollen Blog!
Hallo Menner-Maidi, vielen dank für die tolle Anleitung, bin schwer inspiriert die Lösung für mich umzusetzen. Eine Frage habe ich zu dem Umbau. Hängt durch das Gewicht der Platte und der Fräse der Tisch seitlich nicht etwas ab? Oder anders gefragt ist die Fläche Sägetisch inkl. Multiplexplatte tatsächlich plan, oder muss die Konstruktion seitlich unterbaut werden? Danke für eine Antwort. Gruß Roland
Hei Roland
Hast du die Säge schon bei dir rumstehen? Falls ja, fahr den Parallelanschlag mal maximal aus und klappe die „Auflage“ am Parallelanschlag herunter. Wenn du jetzt eine Wasserwaage/Setzlatte/… plan auf den Sägentisch legst wirst du feststellen, dass die Auflage am Parallelanschlag einige Millimeter tiefer ist. Wenn du jetzt den Parallelanschlag einfährst, ist die Auflage bündig mit dem Sägentisch. Heißt, der Parallelanschlag „hängt“ von Haus aus etwas, vermutlich durch das Spiel das er hat. Das würde aber bedeuten, dass durch den Frästisch nicht viel mehr dazu kommen sollte. Was ich tatsächlich nie getestet habe ist, ob und ggfs. wie viel weiter der Parallelanschlag nach unten hängt, wenn der Frästisch eingehängt ist. Ich probiere das heute Abend mal nachzumessen. Ich melde mich.
Viele Grüße
Andreas
Hallo Roland,
ich war gerade kurz nachmessen. Bei vollausgefahrenem Parallelanschlag ist dieser bei mir rund 2.2mm tiefer als die Arbeitsplatte. Wenn ich den Akkuschrauber auf den Parallelanschlag stelle, hängt dieser rund 3.5mm tiefer, wenn ich den Schlagschrauber drauf stelle (~6kg) hängt der Parallelanschlag 4.5mm tiefer.
Dies war alles ohne eingebauten Frästisch. Wenn ich den Frästisch einbaue, hängt das ganze konstant in jeder Konfiguration ungefähr 1.5mm tiefer.
Es sieht also so aus, als würde zusätzliches Gewicht mehr oder weniger linear dazu führen, dass der Parallelanschlag nach unten nachgibt.
Was ich an der Stelle sagen kann ist, dass, nachdem ich alle „Gewichte“ entfernt habe, wieder die initialen 2.2mm herausgekommen sind.
Wenn man schwerere Platten fräsen will, kann es also durchaus Sinn machen, das ganze abzustützen. Das gilt in dem Fall aber nicht nur für das Fräsen, sondern auch für das Sägen, wenn ein Großteil des Gewichts auf der Auflage am Parallelanschlag liegt.
Jetzt musst natürlich jeder für sich entscheiden, wie oft er mit nahezu vollausgefahrenem Parallelanschlag sägt/fräst. Mit weiter eingefahrenem Parallelanschlag entspannt sich das Problem ja automatisch, da der Hebel kleiner und die Überlappung der Führungsschienen größer wird.
Ich hoffe das hilft dir weiter.
Viele Grüße
Andreas
Hallo Andreas,
Danke für die ausführliche Antwort, ich werde das Projekt mal angehen.
Gruß Roland
Ich wünsch dir viel Erfolg und viel Spaß mit dem Frästisch.
Wenn etwas fehlt /schlecht beschrieben ist/… lass es mich bitte wissen.
Schönes Wochenende
Andreas
Hallo Andreas,
ich sehe Deinen Beitrag als gute Inspiration. Vielen Dank dafür.
Nachdem erst die zweite gelieferte DWE7492 einen akzeptablen planen Tisch hatte und ich nach weiterer zweimaliger Reklamation einen Parallelanschlag erhalten habe der seinem Namen auch entspricht, möchte ich Deine Frästisch-Idee nachbauen.
Was das herunter hängen bei ausgefahrenem Parallelanschlag betrifft:
Das hatte mich auch gestört. Abhilfe habe ich mit einer Teflonplatte (640 x 12 x 0,5 [mm]) geschaffen.
Der Anschlag kann nun ohne „Durchhänger“ komplett ausgefahren werden.
VG
waga
Hallo Namensvetter 🙂
Eieiei, da hast du mit deiner DeWALT aber schon eine ganz schöne Odyssee hinter dir. Hört sich aber so an, als wärst du jetzt zufrieden damit.
Könntest du das mit der Teflonplatte nochmal etwas genauer beschreiben? Wo hast du dein eingebaut, bzw. was macht die Teflonplatte?
Das Durchhägen stört mich nämlich tatsächlich und ich habe bisher noch keinen wirklich praktikablen und flexiblen Workaround gefunden.
Viele Grüße und einen schönen Sonntag
Andreas
Meinen Messungen nach müsste die Teflonplatte auf die obere schwarze Gleitschiene, über die die Parallelanschlagsschienen laufen, geklebt werden.
Bei vollem Auszug ist bei mir dann weder Spiel, noch Durchhängen mehr vorhanden.
Hej, vielen Dank für die tolle Anleitung! Gefällt mir gut und überlege gerade, ob Ich das auch so umsetze.
Mich interessiert, ob es einen bestimmten Grund gibt, dass Du Dir beim Ausschnitt der Einlegeplatte die Mühe mit den einzelnen Bohrungen und dem Rechteckausschnitt gemacht hast? In anderen Anleitungen (für andere Sägen, z.B. auf Youtube LetsBastel für die GTS 10 XC) habe ich gesehen, dass dort vom gefrästen Teil nur ein Steg (breit genug für die die Verschraubung der äußeren Löcher) stehengelassen und der Rest komplett mit der Stichsäge weggesägt wird. Die Fräse wird dann direkt an der Einlegeplatte befestigt – das erlaubt dann auch eine größere Frästiefe.
Guten Abend Nils
Zunächst vielen Dank für das Feedback und die Anregung. Tatsächlich gibt es keinen Grund, weshalb ich die Ausschnitte so aufwändig gemacht habe. Deine Vorschlag, die Platte bis auf die Haltelöcher an der Seite auszuschneiden klingt sogar sehr gut. Wie du sagst, bringt das nochmal 5-10mm mehr Frästiefe. Das nehme ich definitiv in meine „to-do“ Liste mit auf und werde den Frästisch entsprechend anpassen. Vielen Dank nochmal für die Anregung/den Verbesserungsvorschlag.
Viele Grüße
Andreas
Guten Abend lieber Andreas!
Ich hab mir nun auch endlich die dwe7492 bestellt (ist leider noch nicht da) und bin auf der Suche nach einer abnehmbaren Fräsvorrichtung auf deine Seite gestoßen. Ist eine echt coole Sache und ich werd mich demnächst dran machen, um das nachzubauen. Denn auch ich hab nicht all zu viel Platz und kann es daher leider nicht immer drauf lassen.
Ich hätte aber eine (wahrscheinlich laienhafte) Frage. Kann man den Parallelanschlag fürs Fräsen verwenden? Sprich kann man den ein- und ausfahren? Oder hängt man deine Platte quasi bei ausgefahrenem Parallelanschlag ein und dann ist die fix. Vielleicht steh ich auch voll am Schlauch, kann das aber irgendwie auf deinen Fotos nicht so recht erkennen.
Vielen Dank, Christoph.
Guten Morgen Christoph
Freut mich sehr, dass du auf meine Seite gestoßen bist und dir die Idee zusagt.
Den Parallelanschlag kannst du auch für das Fräsen verwenden. Das ist das Gute.
Bisher habe ich mich das noch nicht getraut, aber für die ein oder andere Fräsaufgabe wäre es ganz schön, wenn im Parallelanschlag ein Loch wäre, durch das der Fräser hindurch (bzw. hinein) passt. Wie gesagt, das habe ich mich bisher aber auch noch nicht getraut.
Viel Erfolg beim Umsetzen.
Sollte dir etwas unklar sein oder du einzelne Formulierungen nicht ganz optimal finden, bitte gerne melden.
Andreas